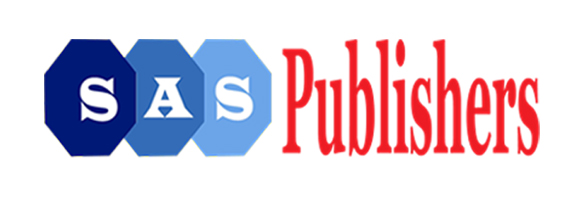
An International Publisher for Academic and Scientific Journals
Author Login
Scholars Journal of Engineering and Technology | Volume-2 | Issue-02
Design and Fabrication of Fault Detecting System Using Robotic Mechanism for Wind Blades
R. Mahendran, Dr.R.Maguteeswaran, A. Joseph Arun Kumar, N.Suresh, S. Thulasi Manikandan
Published: Feb. 22, 2014 |
133
70
DOI: 10.36347/sjet
Pages: 128-133
Downloads
Abstract
Wind blade has to be inspected at regular intervals depends upon the sizes, inspection will be carried out for
every two or four month time intervals. Wind turbine blades are generally built of fiber reinforced plastics and
lightweight materials like plastic foam. High stress are developed in the wind blades due to uneven wind blow, however
the inspections are limited by visual inspections and simple tapping tests. The techniques acquire high levels of
experience and are not able to detect internal damages that are not visible at the surface of the blade. If any defects are
found, blades are re-eraction from the towers by using cranes and maintenance work will carried out separately. Due to
this over all maintenance and operating cost increases, also it requires more labour force and time duration to solve this
problem. To develop a robotic system which inspection unit, locating actuator setup, lighting source, low speed motor,
ultra sonic sensor with CRO interference. This robotic setup does work like fault preventing measures and fault
identifying measures to avoid wind blade failure. The development of non – destructive testing techniques (NDT) for the
use at wind turbine blades would help to make the inspection more reliable. However the testing equipment should be
small and lightweight so that the inspection can be done in service and no need for re-eraction the turbine blades