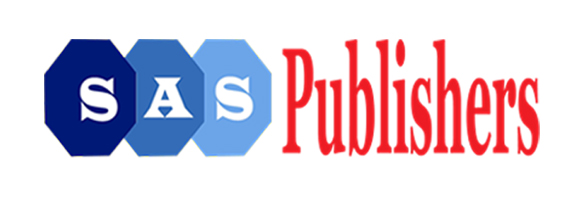
An International Publisher for Academic and Scientific Journals
Author Login
Scholars Journal of Dental Sciences | Volume-4 | Issue-07
Comparison of stress distribution around implants with two different attachments in overdenture supported by four maxillary implants (FEA method)
Dr. Asadallah Ahmadzadeh, Dr.Ahmad Teimouri
Published: July 31, 2017 |
40
48
DOI: 10.36347/sjds.2017.v04i07.003
Pages: 316-322
Downloads
Abstract
As a general rule, the purpose of treatment planning should be minimization and evenly distribution of mechanical stress in the adjacent implant and bone system. Various experimental studies have examined the distribution of stress in the implant supporting bones, thus avoiding the dangers involved. But there is still controversy about biomechanical effects and stress distribution in different attachment designs.The purpose of this study was to compare the distribution of stress around the implant with two different attachments in overdenture based on four maxillary implants using finite element analysis method (FEA). In this experimental study, using the FEA method, a 2D model of maxilla, implant, attachment components and overdenture was first prepared and then, using the ANSYS finite element software, the components of the model were superimposed on each other so that it can act as a component integrated with different materials. These implants were attached to the overdenture using three ball, and locator attachment designs. The 100N force used in this study. Among the two different designs examined, the highest stress was observed in the vertical force (22.87 MPa) imposed on the implant in the right second premolar on the right overdenture supported by the locator implant. In the second place, the highest stress was observed on the Ball-retained overdenture in the right side force, imposed on the implant in the right second premolar corresponding to 12.88 MPa. The least stress among these three designs was observed in the ball-retained overdenture design. Ball-retained overdenture with the lowest stress caused by the 100 N force is the most appropriate design in the present study.